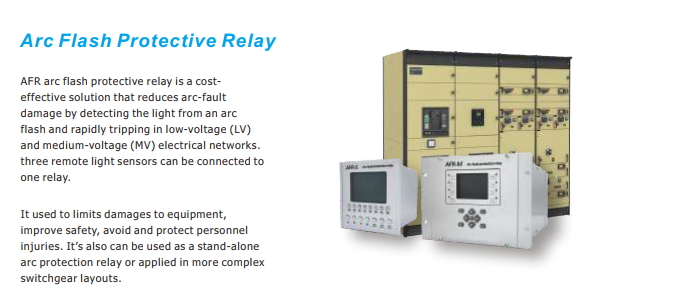
Do You Know About the Latest Electrical Fire Prevention Technology?
Of all the risks that face modern commercial buildings, electrical fires are one of the most common and damaging. Fire endangers health, property and the business itself – half of all organizations that suffer a fire close within the next five years. It’s a danger organization can’t afford to ignore.
Fires can strike at any time and without warning, so businesses should be empowered by the latest technologies to prevent them before they can build to a crisis. Consultant engineers have a real opportunity to show leadership in improving safety, stepping beyond the minimum requirements to protect their business and its most valuable assets.
- Protect against arc faults. There are protective devices that can help reduce the risk of arc faults, by interrupting the current before a fire has a chance to start. An arc fault circuit interrupter (AFCI) will protect a portion of a circuit from parallel (hot to neutral) and series (hot to hot) arcs. For greater protection, a combination arc fault circuit interrupter (CAFCI) can safeguard the entire circuit. Many factors can determine which product is the best fit, including regulations, costs and ease of use. CAFCI circuit breakers remain the choice to provide the best protection, lower installation costs and easily meet all NEC requirements.
Protect against arc flashes. In the USA, an explosion involving an electric arc occurs on average 5 to 6 times a day. Beyond the risk of causing serious physical injuries to personnel (e.g. damage to eyesight, lungs, skin, body impact from the blast), the severe heat and splashes of molten metal from an arc flash can start fires. The best protection against arc flashes are devices that provide ultra-fast detection using a combination of current inputs and light via arc sensor channels. Should a fault occur, the device severs the current to reduce the arc energy released. This not only helps protect people and the availability of the installation, it can also improve the reliability of power distribution protection.

- Take advantage of continuous thermal monitoring technology. As equipment ages, faulty electrical connections in MV and LV installations can increase contact resistance, accelerate deterioration, and eventually create thermal runaway, which can cause a fire, flashover, or explosion. Infrared (IR) thermography has traditionally been used to inspect the highest-risk areas and catch abnormal busbar temperature rises. However, as this is only done when scheduled (e.g. every 12 months) it can miss a connection point that might be deteriorating faster or that was not accessible at the time of inspection. Continuous thermal monitoring technology offers a safer, more comprehensive, and more cost-effective way to detect thermal risks. Wireless thermal sensors are permanently installed on busbar connections, cable connections, and other high-risk points. Temperature data is continuously collected and uploaded to an onsite or cloud-based power management system or power analytics platform, with mobile alerts sent to operations and maintenance teams to help them respond before damage or fire occurs.

Of all the risks that face modern commercial buildings, electrical fires are one of the most common and damaging. Fire endangers health, property and the business itself – half of all organizations that suffer a fire close within the next five years. It’s a danger organization can’t afford to ignore.
Fires can strike at any time and without warning, so businesses should be empowered by the latest technologies to prevent them before they can build to a crisis. Consultant engineers have a real opportunity to show leadership in improving safety, stepping beyond the minimum requirements to protect their business and its most valuable assets.
- Protect against arc faults. There are protective devices that can help reduce the risk of arc faults, by interrupting the current before a fire has a chance to start. An arc fault circuit interrupter (AFCI) will protect a portion of a circuit from parallel (hot to neutral) and series (hot to hot) arcs. For greater protection, a combination arc fault circuit interrupter (CAFCI) can safeguard the entire circuit. Many factors can determine which product is the best fit, including regulations, costs and ease of use. CAFCI circuit breakers remain the choice to provide the best protection, lower installation costs and easily meet all NEC requirements.
Protect against arc flashes. In the USA, an explosion involving an electric arc occurs on average 5 to 6 times a day. Beyond the risk of causing serious physical injuries to personnel (e.g. damage to eyesight, lungs, skin, body impact from the blast), the severe heat and splashes of molten metal from an arc flash can start fires. The best protection against arc flashes are devices that provide ultra-fast detection using a combination of current inputs and light via arc sensor channels. Should a fault occur, the device severs the current to reduce the arc energy released. This not only helps protect people and the availability of the installation, it can also improve the reliability of power distribution protection.
- Take advantage of continuous thermal monitoring technology. As equipment ages, faulty electrical connections in MV and LV installations can increase contact resistance, accelerate deterioration, and eventually create thermal runaway, which can cause a fire, flashover, or explosion. Infrared (IR) thermography has traditionally been used to inspect the highest-risk areas and catch abnormal busbar temperature rises. However, as this is only done when scheduled (e.g. every 12 months) it can miss a connection point that might be deteriorating faster or that was not accessible at the time of inspection. Continuous thermal monitoring technology offers a safer, more comprehensive, and more cost-effective way to detect thermal risks. Wireless thermal sensors are permanently installed on busbar connections, cable connections, and other high-risk points. Temperature data is continuously collected and uploaded to an onsite or cloud-based power management system or power analytics platform, with mobile alerts sent to operations and maintenance teams to help them respond before damage or fire occurs.