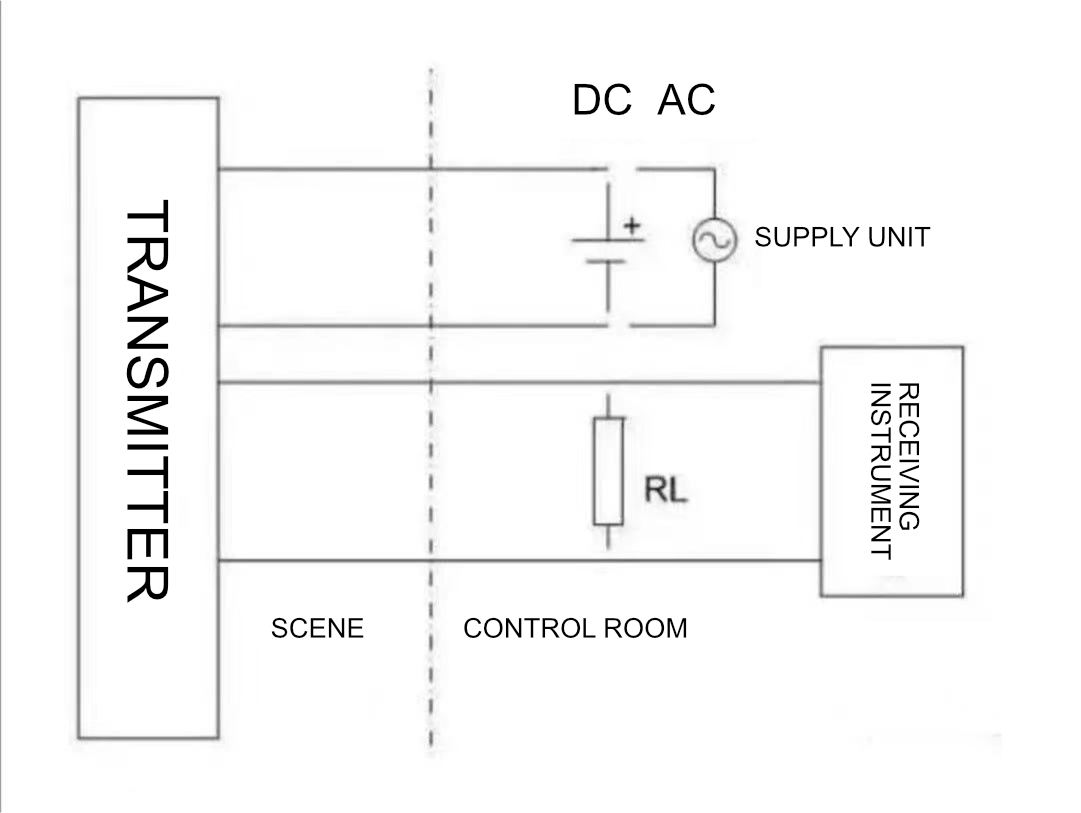
Why the General Industrial Transducer Signal Is 4 to 20 mA?
It is common in the industry to measure various non-electrical physical quantities, such as temperature, pressure, speed, angle, etc., which need to be converted into analog electrical signals before they can be transmitted to a control room or display device hundreds of meters away. This device that converts physical quantities into electrical signals is called a transducer. The most widely used industrial transducer in the industry is to transmit analog quantity with 4~20mA current.
Why does the industrial transducer use a 4-20mA current signal?
The reason for using the current signal is that it is not easily disturbed. Moreover, the internal resistance of the current source is infinite, and the resistance of the wires connected in series in the loop does not affect the accuracy, and the transmission can be hundreds of meters on ordinary twisted-pair wires. The upper limit is 20mA because of explosion-proof requirements: the spark energy caused by the 20mA current on and off is not enough to ignite the gas. The reason why the lower limit is not 0mA is to detect disconnection: it will not be lower than 4mA during normal operation. When the transmission line is disconnected due to a fault, the loop current will drop to 0. 2mA is often taken as the disconnection alarm value.
The current transducer converts the physical quantity into 4~20mA current output and must have an external power supply for it. The most typical is that the transmitter needs two power lines, plus two current output lines, a total of 4 lines are connected, which is called a four-wire transmitter. Of course, the current output can share one wire with the power supply (common VCC or GND), which can save one wire, which is called a three-wire transmitter.
In fact, you may have noticed that the 4-20mA current itself can power the transducer.
The industrial transducer is equivalent to a special load in the circuit. The special feature is that the power consumption current of the industrial transducer varies between 4 and 20mA according to the output of the sensor. The display instrument only needs to be connected in series in the circuit. This kind of industrial transducer only needs 2 external wires, so it is called a two-wire industrial transducer. The lower limit of the industrial current loop standard is 4mA, so as long as it is within the range, the industrial transducer has at least a 4mA power supply. This enables the design of two-wire sensors.
In industrial applications, the measurement point is generally on-site, and the display device or control device is generally in the control room or control cabinet. The distance between the two may be tens to hundreds of meters. Calculated at a distance of 100 meters, saving 2 wires means that the cost is reduced by nearly 100 yuan! Therefore, the two-wire sensor must be the first choice in the application.
The structure and principle of the two-wire industrial transducer
The principle of the two-wire industrial transducer is to use the 4~20mA signal to provide electric energy for itself. If the transducer itself consumes more than 4mA, it will be impossible to output the lower limit 4mA value. Therefore, it is generally required that the power consumption of the two-wire transmitter itself (all circuits including the sensor) should not exceed 3.5mA. This is one of the fundamental principles behind the design of two-wire industrial transducers. From the perspective of the overall structure, the two-wire industrial transducer consists of three major parts: sensors, conditioning circuits, and two-wire V/I converters. The sensor converts physical quantities such as temperature and pressure into electrical parameters, and the conditioning circuit amplifies, adjusts, and converts the weak or nonlinear electrical signal output by the sensor into a linear voltage output.
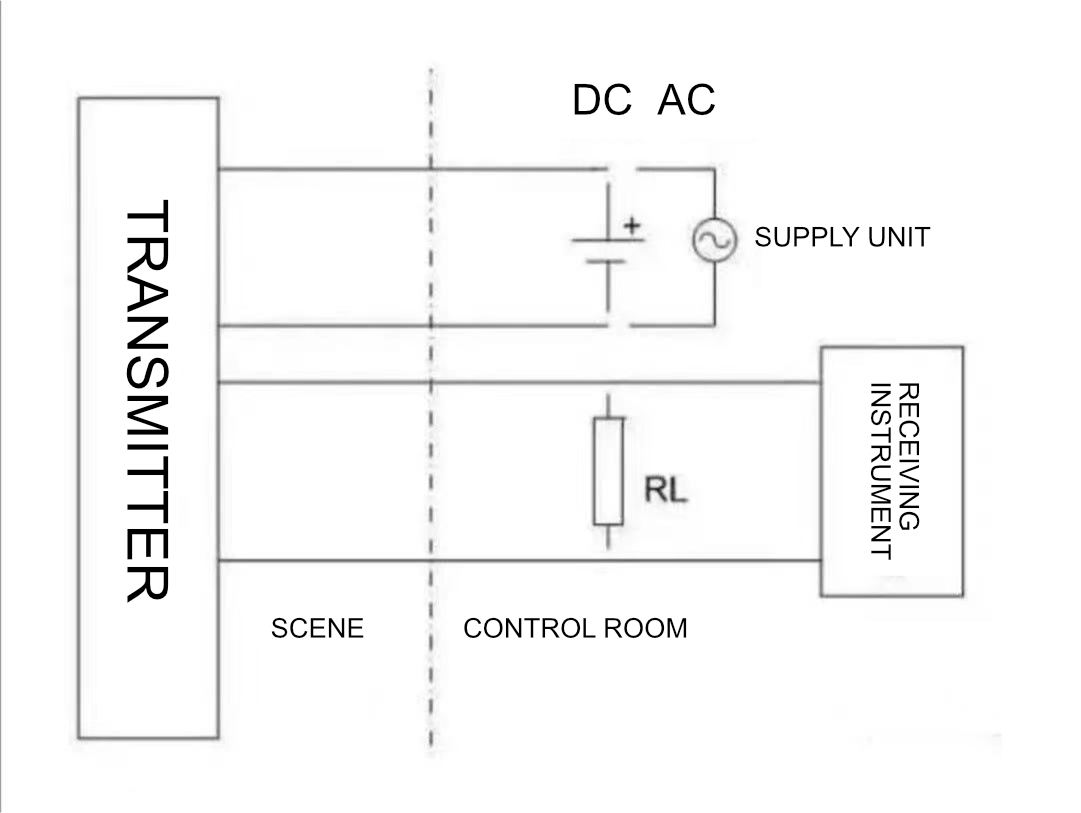
The two-wire V/I conversion circuit controls the overall power consumption current according to the output of the signal conditioning circuit; at the same time, it obtains and stabilizes the voltage from the loop for use by the conditioning circuit and sensors. In addition to the V/I conversion circuit, each part of the circuit has its own power consumption current. The core design idea of the two-wire industrial transducer is to include all currents in the feedback loop of the V/I conversion. As shown in the figure, the sampling resistor Rs is connected in series at the low end of the circuit, and all the current will flow back to the negative pole of the power supply through Rs. The feedback signal obtained from Rs includes the power consumption of all circuits. In a two-wire transmitter, the total power consumption of all circuits cannot exceed 3.5mA, so the low power consumption of the circuit becomes the main design difficulty. The principle and design points of each part of the circuit will be analyzed one by one below.
Two-wire V/I converter The V/I converter is a circuit that can control the output current with a voltage signal. The difference between the two-wire V/I converter and the general V/I conversion circuit is that the voltage signal does not directly control the output current, but controls the power consumption current of the entire circuit itself. At the same time, a stable voltage must be extracted from the current loop to power the conditioning circuit and sensors. The accompanying drawing is the basic principle diagram of the two-wire V/I conversion circuit: OP1, Q1, R1, R2, and Rs in the figure constitute the V/I converter. Analyze the negative feedback process: If point A is higher than 0V for some reason, the output of op amp OP1 will increase, the voltage across Re will increase, and the current passing through Re will increase. It means that the overall power consumption becomes larger, the current through the sampling resistor Rs also becomes larger, and the voltage at point B becomes lower (more negative). The result is that the voltage at point A is pulled down through R2. Conversely, if point A is lower than 0V for some reason, it will be raised back to 0V by negative feedback. In short, the result of negative feedback is that the operational amplifier OP1 is virtual short, and the voltage at point A = 0V.
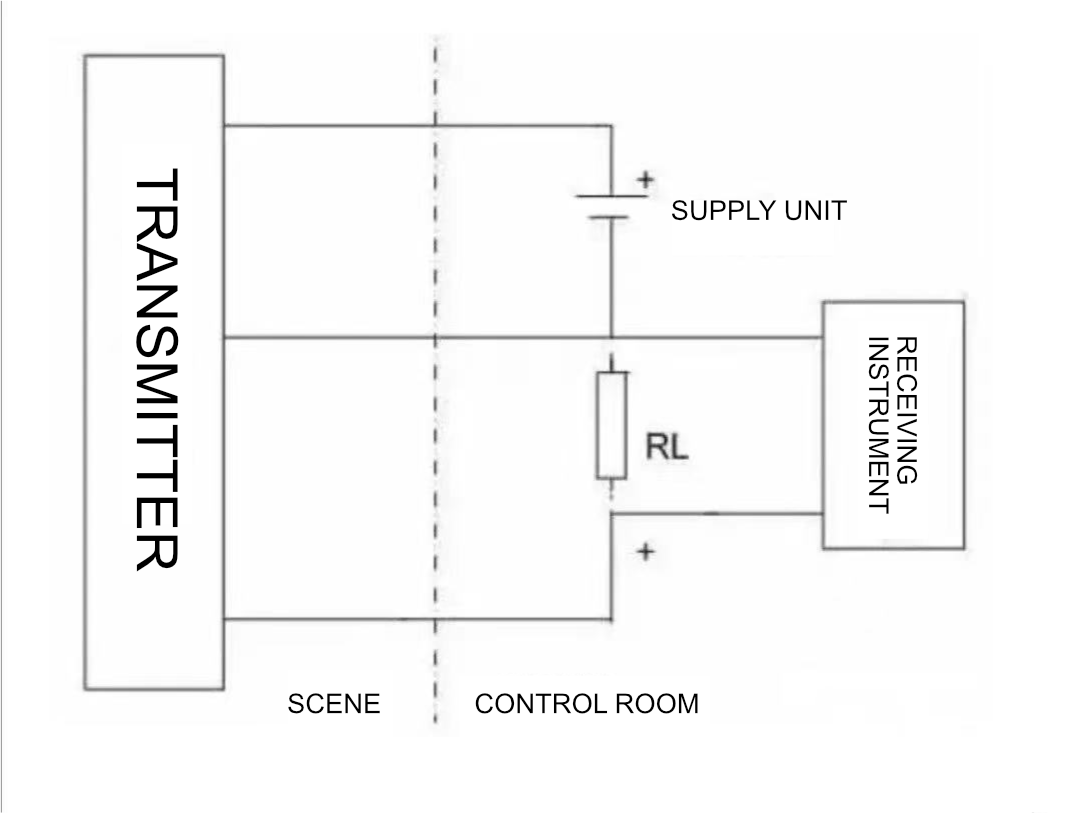
The control principle of Vo on the total power consumption is analyzed below: Assuming that the output voltage of the conditioning circuit is Vo, the current flowing through R1 I1=Vo/R1, the input terminal of the operational amplifier cannot absorb current, and all I1 flows through R2, then the voltage at point B VB= -I1*R2 = -Vo*R2/R1 When R1=R2, VB=-Vo There are only two resistors, Rs and R2, between the negative power supply and the entire transmitter circuit, so all the current flows through Rs and R2. The upper end of R2 is a virtual ground (0V), and the upper end of Rs is GND. Therefore, the voltages at both ends of R2 and Rs are exactly the same, equal to VB. It is equivalent to connecting Rs and R2 in parallel as a current sampling resistor. Therefore, the total current of the circuit: Is=Vo/(Rs//R2) If R2>>Rs is taken, Is=Vo/Rs Therefore, in Figure 3, Rs=100 ohms, when the conditioning circuit outputs 0.4~2V, the total power consumption Electric current 4~20mA. It doesn’t matter if R2>>Rs cannot be satisfied, Rs and R2 are connected in parallel (Rs//R2) is a fixed value, Is and Vo are still linear, and the error proportional coefficient can be eliminated during calibration.
In addition to the correct circuit, two conditions are required for the normal operation of the circuit: first, the power consumption must be as small as possible, and the saved current must be supplied to the conditioning circuit and the transmitter. Secondly, it is required that the op amp can work with a single power supply, that is, in the absence of a negative power supply, the input terminal can still accept 0V input and work normally. LM358/324 is the most common and cheapest single-supply op amp, with a power consumption of 400uA per op-amp, which is basically acceptable. When powered by a single power supply, the input terminal can work normally from -0.3V~Vcc-1.5V. If it is replaced with a precision amplifier such as OP07, because the input is not allowed to be as low as 0V, it will not work in this circuit. R5 and U1 constitute the reference source, which generates a stable reference voltage of 2.5V. LM385 is a low-cost micro-power consumption reference, and it can work with more than 20uA. The curve given in the manual is the flattest around 100uA, so the current control current is about 100uA through R5. OP2 constitutes a non-inverting amplifier, which amplifies the reference and supplies power to the conditioning circuit and the sensor. Because voltage regulators with wide input voltage and low power consumption are scarce and cost high; it is a cheap solution to use the reference amplifier as a regulated power supply. This part of the circuit can also choose off-the-shelf integrated circuits. For example, XTR115/116/105, etc., have better accuracy and stability than self-made ones, and their own power consumption is also lower (meaning more current can be left for the conditioning circuit, and the conditioning part is easier to design). But the cost is more than 10 times higher than the above scheme.
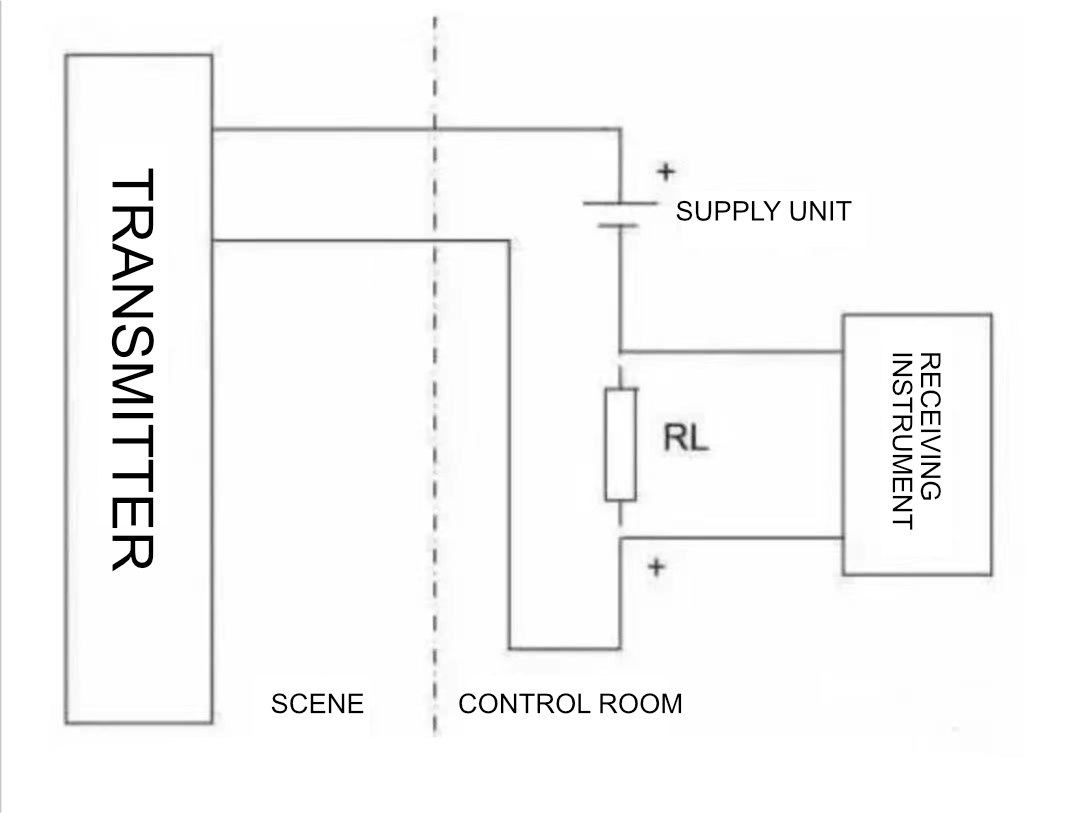
Two-wire pressure industrial transducer design The output signals of the pressure bridge and the load cell are weak, and they all belong to the mV level signal. This type of small signal generally requires a differential amplifier to amplify it in the first stage. Generally, a differential amplifier with low offset and low-temperature drift is selected. In addition, in two-wire applications, low power consumption is also required. AD623 is a commonly used low-power precision differential amplifier, which is commonly used in the amplification of the differential output front stage. The maximum offset of AD623 is 200uV, and the temperature drift is 1uV/degree, which ensures sufficient accuracy in general pressure transmission applications. R0 superimposes 0.4V on the REF pin (pin 5) of AD623. When the pressure is 0, adjust R0 to output 4mA, and then adjust RG to output 20.00mA to complete the calibration. When designing the circuit, it should be noted that the pressure bridge sensor is equivalent to a kiloohm-level resistor, and generally consumes a lot of power. Appropriately reducing the excitation voltage of the pressure bridge can reduce the power consumption current. However, the output amplitude also decreases, and the gain of AD623 needs to be increased. The sensor shown in Figure 6 uses a constant voltage power supply. In practical applications, most semiconductor pressure sensors need a constant current power supply to obtain better temperature characteristics. An operational amplifier can be used to form a constant current source to provide excitation for it.
Stability and safety considerations The environment in industrial environment is harsh and requires high reliability, so the design of the two-wire industrial transducer needs to consider certain protection and stability enhancement measures.
1. Power protection.
Reverse connection of power supply, overvoltage, and surge are common power supply problems in the industry. A reverse connection of the power supply is the most common mistake when installing and wiring the equipment. A diode connected to the input port can prevent the circuit from being damaged when the power supply is connected reversely. If a full-bridge rectifier is added to the input, it can still work normally even if the power supply is reversed. In order to prevent lightning, electrostatic discharge, surge, and other energy from damaging the transmitter, a TVS tube can be installed at the inlet of the transmitter to absorb the energy of instantaneous overvoltage. Generally, the TVS voltage value is slightly lower than the limit voltage of the op-amp to play a protective role. If it is possible to be struck by lightning, the TVS may not have enough absorption capacity, and the varistor is also necessary, but the leakage of the varistor itself will cause a certain error.
2. overcurrent protection
During the operation of the equipment, errors such as sensor disconnection and short circuits may occur. Or the input itself is likely to exceed the range, and the transmitter must ensure that the output will not rise without limit under any circumstances, otherwise, it may damage the transmitter itself, the power supply, or the remote display instrument. In the figure, Rb and Z1 constitute an overcurrent protection circuit. No matter what causes the output of OP1 to be greater than 6.2V (1N4735 is a 6.2V regulator tube), it will be clamped by Z1, and the base of Q1 cannot be higher than 6.2V. Therefore, the voltage on Re cannot be higher than 6.2-0.6=5.6V, so the total current will not be greater than Ue/Re = 5.6V/200=28mA.
3. Wide voltage adaptability
Generally, two-wire transmitters can adapt to a wide range of voltage changes without affecting accuracy. In this way, it can be applied to various power sources and can adapt to large load resistances at the same time. The most sensitive part of the power supply is the reference source, and the reference source is also the main component that determines the accuracy. In Figure 3, the reference current is limited by R5. When the power supply voltage changes, the current on R5 also changes, which has a great impact on the stability of the reference. In the figure, the constant current source LM334 is used as the reference power supply. When the voltage changes in a large range, the current basically remains unchanged, which ensures the stability of the reference.
4. Decoupling Capacitor In general circuit design
There will be a decoupling capacitor on the power supply side of each integrated circuit. When the two-wire transmitter is powered on, the charging of these capacitors will cause a large current in an instant, which may damage the remote instrument. Therefore, each decoupling capacitance generally does not exceed 10nF, and the total decoupling capacitance should not exceed 50nF. A 10nF capacitor at the entrance is required to ensure that the circuit does not oscillate under long-line inductive loads.
It is common in the industry to measure various non-electrical physical quantities, such as temperature, pressure, speed, angle, etc., which need to be converted into analog electrical signals before they can be transmitted to a control room or display device hundreds of meters away. This device that converts physical quantities into electrical signals is called a transducer. The most widely used industrial transducer in the industry is to transmit analog quantity with 4~20mA current.
Why does the industrial transducer use a 4-20mA current signal?
The reason for using the current signal is that it is not easily disturbed. Moreover, the internal resistance of the current source is infinite, and the resistance of the wires connected in series in the loop does not affect the accuracy, and the transmission can be hundreds of meters on ordinary twisted-pair wires. The upper limit is 20mA because of explosion-proof requirements: the spark energy caused by the 20mA current on and off is not enough to ignite the gas. The reason why the lower limit is not 0mA is to detect disconnection: it will not be lower than 4mA during normal operation. When the transmission line is disconnected due to a fault, the loop current will drop to 0. 2mA is often taken as the disconnection alarm value.
The current transducer converts the physical quantity into 4~20mA current output and must have an external power supply for it. The most typical is that the transmitter needs two power lines, plus two current output lines, a total of 4 lines are connected, which is called a four-wire transmitter. Of course, the current output can share one wire with the power supply (common VCC or GND), which can save one wire, which is called a three-wire transmitter.
In fact, you may have noticed that the 4-20mA current itself can power the transducer.
The industrial transducer is equivalent to a special load in the circuit. The special feature is that the power consumption current of the industrial transducer varies between 4 and 20mA according to the output of the sensor. The display instrument only needs to be connected in series in the circuit. This kind of industrial transducer only needs 2 external wires, so it is called a two-wire industrial transducer. The lower limit of the industrial current loop standard is 4mA, so as long as it is within the range, the industrial transducer has at least a 4mA power supply. This enables the design of two-wire sensors.
In industrial applications, the measurement point is generally on-site, and the display device or control device is generally in the control room or control cabinet. The distance between the two may be tens to hundreds of meters. Calculated at a distance of 100 meters, saving 2 wires means that the cost is reduced by nearly 100 yuan! Therefore, the two-wire sensor must be the first choice in the application.
The structure and principle of the two-wire industrial transducer
The principle of the two-wire industrial transducer is to use the 4~20mA signal to provide electric energy for itself. If the transducer itself consumes more than 4mA, it will be impossible to output the lower limit 4mA value. Therefore, it is generally required that the power consumption of the two-wire transmitter itself (all circuits including the sensor) should not exceed 3.5mA. This is one of the fundamental principles behind the design of two-wire industrial transducers. From the perspective of the overall structure, the two-wire industrial transducer consists of three major parts: sensors, conditioning circuits, and two-wire V/I converters. The sensor converts physical quantities such as temperature and pressure into electrical parameters, and the conditioning circuit amplifies, adjusts, and converts the weak or nonlinear electrical signal output by the sensor into a linear voltage output.
The two-wire V/I conversion circuit controls the overall power consumption current according to the output of the signal conditioning circuit; at the same time, it obtains and stabilizes the voltage from the loop for use by the conditioning circuit and sensors. In addition to the V/I conversion circuit, each part of the circuit has its own power consumption current. The core design idea of the two-wire industrial transducer is to include all currents in the feedback loop of the V/I conversion. As shown in the figure, the sampling resistor Rs is connected in series at the low end of the circuit, and all the current will flow back to the negative pole of the power supply through Rs. The feedback signal obtained from Rs includes the power consumption of all circuits. In a two-wire transmitter, the total power consumption of all circuits cannot exceed 3.5mA, so the low power consumption of the circuit becomes the main design difficulty. The principle and design points of each part of the circuit will be analyzed one by one below.
Two-wire V/I converter The V/I converter is a circuit that can control the output current with a voltage signal. The difference between the two-wire V/I converter and the general V/I conversion circuit is that the voltage signal does not directly control the output current, but controls the power consumption current of the entire circuit itself. At the same time, a stable voltage must be extracted from the current loop to power the conditioning circuit and sensors. The accompanying drawing is the basic principle diagram of the two-wire V/I conversion circuit: OP1, Q1, R1, R2, and Rs in the figure constitute the V/I converter. Analyze the negative feedback process: If point A is higher than 0V for some reason, the output of op amp OP1 will increase, the voltage across Re will increase, and the current passing through Re will increase. It means that the overall power consumption becomes larger, the current through the sampling resistor Rs also becomes larger, and the voltage at point B becomes lower (more negative). The result is that the voltage at point A is pulled down through R2. Conversely, if point A is lower than 0V for some reason, it will be raised back to 0V by negative feedback. In short, the result of negative feedback is that the operational amplifier OP1 is virtual short, and the voltage at point A = 0V.
The control principle of Vo on the total power consumption is analyzed below: Assuming that the output voltage of the conditioning circuit is Vo, the current flowing through R1 I1=Vo/R1, the input terminal of the operational amplifier cannot absorb current, and all I1 flows through R2, then the voltage at point B VB= -I1*R2 = -Vo*R2/R1 When R1=R2, VB=-Vo There are only two resistors, Rs and R2, between the negative power supply and the entire transmitter circuit, so all the current flows through Rs and R2. The upper end of R2 is a virtual ground (0V), and the upper end of Rs is GND. Therefore, the voltages at both ends of R2 and Rs are exactly the same, equal to VB. It is equivalent to connecting Rs and R2 in parallel as a current sampling resistor. Therefore, the total current of the circuit: Is=Vo/(Rs//R2) If R2>>Rs is taken, Is=Vo/Rs Therefore, in Figure 3, Rs=100 ohms, when the conditioning circuit outputs 0.4~2V, the total power consumption Electric current 4~20mA. It doesn’t matter if R2>>Rs cannot be satisfied, Rs and R2 are connected in parallel (Rs//R2) is a fixed value, Is and Vo are still linear, and the error proportional coefficient can be eliminated during calibration.
In addition to the correct circuit, two conditions are required for the normal operation of the circuit: first, the power consumption must be as small as possible, and the saved current must be supplied to the conditioning circuit and the transmitter. Secondly, it is required that the op amp can work with a single power supply, that is, in the absence of a negative power supply, the input terminal can still accept 0V input and work normally. LM358/324 is the most common and cheapest single-supply op amp, with a power consumption of 400uA per op-amp, which is basically acceptable. When powered by a single power supply, the input terminal can work normally from -0.3V~Vcc-1.5V. If it is replaced with a precision amplifier such as OP07, because the input is not allowed to be as low as 0V, it will not work in this circuit. R5 and U1 constitute the reference source, which generates a stable reference voltage of 2.5V. LM385 is a low-cost micro-power consumption reference, and it can work with more than 20uA. The curve given in the manual is the flattest around 100uA, so the current control current is about 100uA through R5. OP2 constitutes a non-inverting amplifier, which amplifies the reference and supplies power to the conditioning circuit and the sensor. Because voltage regulators with wide input voltage and low power consumption are scarce and cost high; it is a cheap solution to use the reference amplifier as a regulated power supply. This part of the circuit can also choose off-the-shelf integrated circuits. For example, XTR115/116/105, etc., have better accuracy and stability than self-made ones, and their own power consumption is also lower (meaning more current can be left for the conditioning circuit, and the conditioning part is easier to design). But the cost is more than 10 times higher than the above scheme.
Two-wire pressure industrial transducer design The output signals of the pressure bridge and the load cell are weak, and they all belong to the mV level signal. This type of small signal generally requires a differential amplifier to amplify it in the first stage. Generally, a differential amplifier with low offset and low-temperature drift is selected. In addition, in two-wire applications, low power consumption is also required. AD623 is a commonly used low-power precision differential amplifier, which is commonly used in the amplification of the differential output front stage. The maximum offset of AD623 is 200uV, and the temperature drift is 1uV/degree, which ensures sufficient accuracy in general pressure transmission applications. R0 superimposes 0.4V on the REF pin (pin 5) of AD623. When the pressure is 0, adjust R0 to output 4mA, and then adjust RG to output 20.00mA to complete the calibration. When designing the circuit, it should be noted that the pressure bridge sensor is equivalent to a kiloohm-level resistor, and generally consumes a lot of power. Appropriately reducing the excitation voltage of the pressure bridge can reduce the power consumption current. However, the output amplitude also decreases, and the gain of AD623 needs to be increased. The sensor shown in Figure 6 uses a constant voltage power supply. In practical applications, most semiconductor pressure sensors need a constant current power supply to obtain better temperature characteristics. An operational amplifier can be used to form a constant current source to provide excitation for it.
Stability and safety considerations The environment in industrial environment is harsh and requires high reliability, so the design of the two-wire industrial transducer needs to consider certain protection and stability enhancement measures.
1. Power protection.
Reverse connection of power supply, overvoltage, and surge are common power supply problems in the industry. A reverse connection of the power supply is the most common mistake when installing and wiring the equipment. A diode connected to the input port can prevent the circuit from being damaged when the power supply is connected reversely. If a full-bridge rectifier is added to the input, it can still work normally even if the power supply is reversed. In order to prevent lightning, electrostatic discharge, surge, and other energy from damaging the transmitter, a TVS tube can be installed at the inlet of the transmitter to absorb the energy of instantaneous overvoltage. Generally, the TVS voltage value is slightly lower than the limit voltage of the op-amp to play a protective role. If it is possible to be struck by lightning, the TVS may not have enough absorption capacity, and the varistor is also necessary, but the leakage of the varistor itself will cause a certain error.
2. overcurrent protection
During the operation of the equipment, errors such as sensor disconnection and short circuits may occur. Or the input itself is likely to exceed the range, and the transmitter must ensure that the output will not rise without limit under any circumstances, otherwise, it may damage the transmitter itself, the power supply, or the remote display instrument. In the figure, Rb and Z1 constitute an overcurrent protection circuit. No matter what causes the output of OP1 to be greater than 6.2V (1N4735 is a 6.2V regulator tube), it will be clamped by Z1, and the base of Q1 cannot be higher than 6.2V. Therefore, the voltage on Re cannot be higher than 6.2-0.6=5.6V, so the total current will not be greater than Ue/Re = 5.6V/200=28mA.
3. Wide voltage adaptability
Generally, two-wire transmitters can adapt to a wide range of voltage changes without affecting accuracy. In this way, it can be applied to various power sources and can adapt to large load resistances at the same time. The most sensitive part of the power supply is the reference source, and the reference source is also the main component that determines the accuracy. In Figure 3, the reference current is limited by R5. When the power supply voltage changes, the current on R5 also changes, which has a great impact on the stability of the reference. In the figure, the constant current source LM334 is used as the reference power supply. When the voltage changes in a large range, the current basically remains unchanged, which ensures the stability of the reference.
4. Decoupling Capacitor In general circuit design
There will be a decoupling capacitor on the power supply side of each integrated circuit. When the two-wire transmitter is powered on, the charging of these capacitors will cause a large current in an instant, which may damage the remote instrument. Therefore, each decoupling capacitance generally does not exceed 10nF, and the total decoupling capacitance should not exceed 50nF. A 10nF capacitor at the entrance is required to ensure that the circuit does not oscillate under long-line inductive loads.