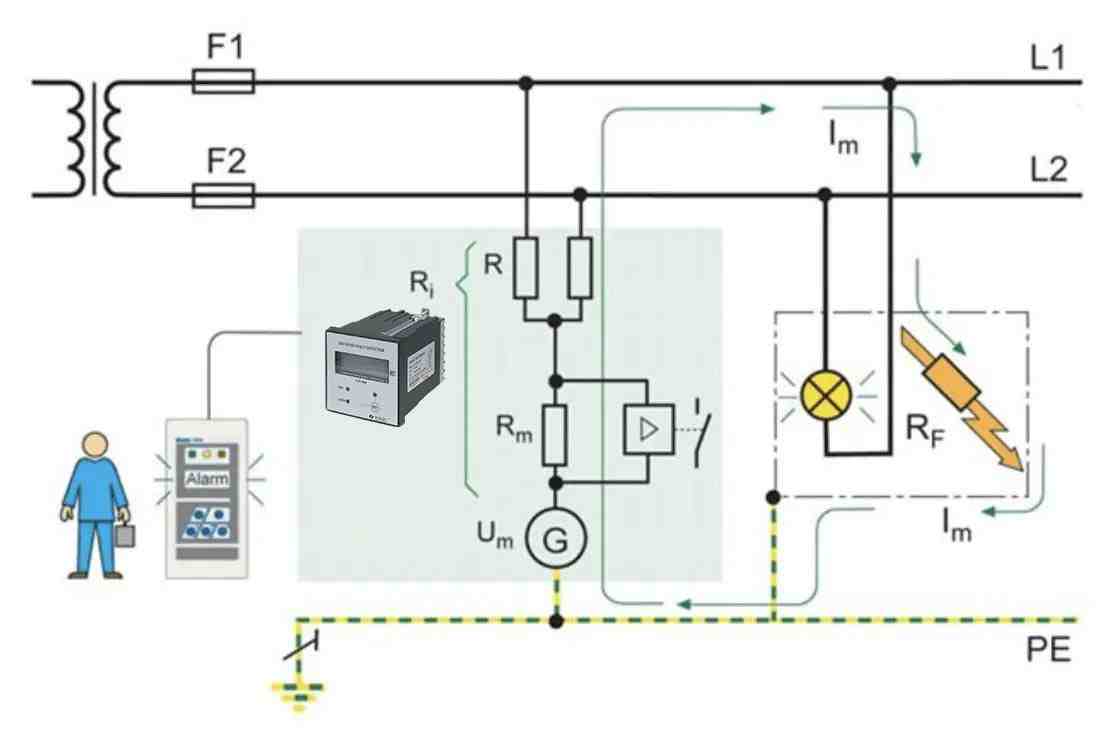
Insulation Resistance Monitoring and Measuring
As Insulation resistance is important in electrical equipment, this
CAN communication is widely used in DC insulation monitoring devices now. This article will introduce the CAN communication for DC insulation monitoring devices.
CAN communication for DC insulation monitoring devices refer to using the Controller Area Network (CAN) protocol for data exchange between the DC insulation monitor and other system equipment.
High reliability and Real-time Data
The CAN communication uses error detection and correction mechanisms to ensure reliable data transmission. CAN prioritizes messages based on importance, allowing for real-time transmission of critical data like insulation resistance measurements.
Multi-node communication
A CAN bus allows multiple devices to connect and communicate at the same time, and each node can send and receive data independently. This allows the DC insulation monitoring device to exchange data with multiple system components such as battery management systems, charge controllers, display units, etc.
Simplified wiring
The CAN communication adopts a twisted pair structure, which can significantly reduce the complexity and cost of wiring. This is very beneficial for insulation monitor integration and maintenance, especially in complex electrical systems.
Data protocol
The DC insulation monitoring systems commonly used CAN data protocols include CANopen and SAE J1939.
CANopen is a general CAN application layer protocol suitable for communication between various devices. The CANopen protocol defines concepts such as device configuration files, object dictionaries, and service data objects, and specifies message formats and data identifiers.
SAE J1939 is a CAN application layer protocol dedicated to commercial vehicles and agricultural machinery. The SAE J1939 protocol defines concepts such as device type, PGN (Parameter Group Number), CAN ID, etc., and stipulates message formats and data identifiers.
Message structure
CAN messages are the basic unit of CAN communication and are used to transfer data between devices. In DC insulation monitoring systems, CAN messages usually contain the following information:
Device ID: Identifies the device sending the message.
Insulation resistance value: DC side insulation resistance value measured by the insulation monitor.
Voltage measurement value: DC side voltage value measured by the insulation monitor.
Status flag: Indicates the status of the insulation monitor, such as normal, alarm, fault, etc.
Communication example
An insulation monitor might periodically transmit a CAN message containing the measured DC side insulation resistance. A central controller or monitoring system can receive this message and take appropriate actions based on the value (e.g., trigger an alarm if resistance falls below a threshold).
For DC insulation monitoring, CAN communication shines in real-time critical data transfer with prioritization and multi-device support. Modbus, while simpler to implement and potentially cost-effective, is better for limited devices and may experience delays due to its polling nature. CAN requires additional protocol layers like CANopen for functionality, but offers robust error detection. Both can be cost-effective, with the choice depending on specific needs for real-time performance and scalability.
Feature | CAN | Modbus |
Protocol Type | Multi-master, message-based | Master-slave, request-response based |
Data prioritization | Supports message prioritization for critical data | No prioritization, all messages treated equally |
Real-time performance | Well-suited for real-time data transmission | Can introduce delays due to polling nature |
Multi-device support | Supports connecting many devices to a single bus | Limited number of devices per bus segment (typically 32) |
Error detection | Built-in error detection and correction mechanisms | Relies on error checking within the application layer |
Cost | Generally cost-effective due to mature technology | Can be cost-effective, but additional configuration might be needed |
Complexity | Requires additional protocol implementation (CANopen, SAE J1939) | Relatively simpler to implement |
Blue Jay offers DC insulation monitoring devices with CAN Communication or RS485 communication. Our GYID series DC insulation monitoring device uses CAN communication, which is widely used for electrical vehicles. Our ZJS series, ZJJ series, and GY series use RS485 communication, which is used for DC Systems, It systems, EV charger stations, etc.
DC Insulation Monitoring Device With CanBus communication
High safety for electrical vehicle insulation monitoring. EV battery insulation monitoring. CE cerfitifaction Approved!
As Insulation resistance is important in electrical equipment, this
Insulation monitor is widely used in DC Charging Stations, DC
Abstract: This article will introduce the RS485 communication protocol