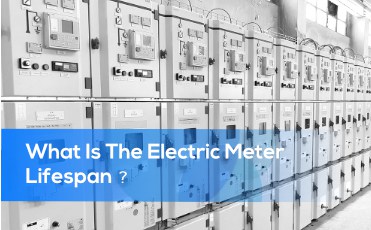
What Is the Electric Meter Lifespan?
What is Blue Jay Technology Electric meter lifespan? It is between 5 years and 10 years. besides, you can learn the factors that affect the electric meter lifespan.
Profibus (Process Fieldbus), as a communication protocol in industrial automation systems, uses master-slave architecture and serial communication to achieve efficient data exchange and control command transmission between various field devices, sensors and actuators.
Detailed explanation of the master-slave architecture: The master station is responsible for controlling the communication process and realizing the transmission of data frames by regularly polling the connected slave stations. This structure ensures coordinated and real-time communication.
Serial communication technology: Using serial communication, using physical layer standards such as RS-485, efficient industrial communication is achieved through the transmission of data frames. The advantage of serial communication is that it reduces cable costs and improves anti-interference performance.
Frame structure analysis: Data frame consists of frame header, data field and frame trailer. The frame header identifies the beginning of the data frame, the data field contains the actual data information, and the frame trailer marks the end of the data frame. This structure facilitates flexible data exchange.
Detailed introduction to Profibus-DP: Profibus-DP is mainly used for high-speed data exchange and is suitable for communication between PLC and distributed peripheral devices. Its fast data transfer rates and low latency performance make it stand out in industrial environments that require real-time control and high levels of integration.
Analysis of Profibus-PA features: Profibus-PA is specially used in process automation fields, such as chemical and petrochemical industries. It is characterized by adapting to work in harsh environmental conditions and providing highly reliable communications to meet high requirements for safety and stability.
Detailed comparison of DPV1 and DPV2 versions: The DPV1 version provides more features and enhanced performance relative to the basic Profibus-DP. The DPV2 version further improves the functionality, introduces more powerful diagnostic and device management functions, and improves the maintainability of the system.
Specific applications in manufacturing: In manufacturing, Profibus connects PLCs, sensors and actuators to achieve efficient control of the production process. For example, in automated assembly lines, Profibus can be used to coordinate the movement of robots and conveyor belts.
Practical examples in process automation: In the field of process automation, such as chemical and refinery plants, Profibus ensures real-time control of various sensors and actuators to maintain a high degree of accuracy in critical processes.
Application scenarios in public utilities: In the field of public utilities, such as water treatment plants, Profibus is used to coordinate the operation of water pumps, valves and other equipment to ensure efficient and stable operation of the system.
The role of the communication backbone: Profibus, as the communication backbone between PLC and field equipment, achieves efficient data exchange and provides a stable foundation for the automation process.
An in-depth look at data exchange: Profibus enables PLCs to conduct flexible data exchange with multiple devices, including sensors and actuators, thus achieving a high degree of integration in automation systems.
Profibus communication is a standardized protocol for seamless data exchange and control command transmission in industrial automation systems. Derived from the “process fieldbus”, Profibus uses a master-slave architecture and serial communications to facilitate efficient real-time communication between various field devices, sensors, actuators and controllers.
Master-Slave Architecture: Profibus operates on a master-slave architecture, where the master controls the communication process by cyclically polling each connected slave, ensuring coordinated data exchange.
Serial Communication: Profibus uses serial communication, usually based on standards such as RS-485. This serial communication increases the efficiency and reduces complexity of communication lines in industrial environments.
Frame structure: Communication in Profibus is organized into frames, including frame headers, data fields, and frame trailers. This structured approach allows flexible configuration to meet specific communication needs.
Cyclic Data Exchange: Profibus communication involves cyclic data exchange between a master and slaves, with the master initiating the communication cycle by polling each slave for data or command execution.
Error detection and correction: Profibus incorporates error detection and correction mechanisms, such as CRC (Cyclic Redundancy Check), to ensure the reliability of communications by identifying and correcting errors during transmission.
Flexible communication rates: Profibus supports different communication rates, allowing flexible configuration according to specific system requirements, affecting the speed of data transmission.
Real-time communication: Profibus is designed to provide real-time communication, making it suitable for applications where timing and synchronization are critical to the proper functioning of the automated process.
Nonfieldbus Systems Overview: Nonfieldbus systems generally refer to traditional communications architectures that may rely on point-to-point wiring, parallel communication lines, or proprietary protocols. These systems often lack the advanced functionality and flexibility offered by fieldbus technology.
PROFIBUS System Details: PROFIBUS, on the other hand, represents a fieldbus technology known for its standardized communication protocol. It adopts a master-slave architecture to ensure synchronous and efficient communication between various devices in the industrial network.
Advantages of PROFIBUS systems:
Interoperability: PROFIBUS systems provide excellent interoperability, allowing devices from different manufacturers to be seamlessly integrated into the network.
Real-time communication: PROFIBUS ensures real-time communication, supporting applications that require precise timing and synchronization.
Flexibility: The flexibility of the PROFIBUS system enables efficient connection of different devices, helping to improve the overall adaptability of the industrial automation system.
Challenges of non-fieldbus systems:
Limited flexibility: Non-fieldbus systems may lack the flexibility to adapt to changing industrial automation requirements, potentially leading to system upgrade challenges.
Complex wiring: These systems often involve complex wiring structures, which can lead to increased installation and maintenance efforts.
Scalability considerations: PROFIBUS systems are generally more scalable, allowing devices to be easily added without major modifications to existing infrastructure. This scalability is beneficial for industries that are experiencing growth or changing automation needs.
PROFIBUS and Profinet are both industrial communication protocols developed by PROFIBUS & PROFINET International (PI). However, they serve different purposes and have different characteristics.
PROFIBUS overview: PROFIBUS was established earlier and is a mature fieldbus communication protocol designed for various industrial applications. It is known for its real-time capabilities and powerful performance in manufacturing and process automation.
Profinet Overview: Profinet, on the other hand, is a recent addition and represents the transition from fieldbus to industrial Ethernet. Profinet offers higher communication speeds and greater flexibility, making it suitable for applications requiring advanced networking capabilities.
Communication technology: PROFIBUS uses traditional fieldbus technology and adopts a master-slave architecture, while Profinet is based on industrial Ethernet, which can achieve faster and more efficient communication.
Data transfer speed: Profinet generally supports higher data transfer speeds compared to PROFIBUS, making it suitable for applications where high-speed communication is critical.
Integration with IT systems: Profinet’s use of industrial Ethernet facilitates better integration with IT systems and enables seamless communication between industrial and enterprise networks.
Device Integration: While PROFIBUS has matured and has a large number of supported devices, Profinet has also grown in popularity and its device ecosystem continues to grow.
Application Notes: PROFIBUS remains a solid choice for applications with proven fieldbus requirements, while Profinet is favored in scenarios that require advanced networking capabilities and integration with higher-level enterprise systems.
The choice between PROFIBUS and Profinet depends on the specific application requirements, with PROFIBUS meeting the given industrial automation needs, while Profinet offers a more modern and flexible solution with higher communication speeds.
PROFIBUS and Modbus are both widely used communication protocols in the field of industrial automation, each with its own characteristics and applications.
PROFIBUS Overview: As mentioned earlier, PROFIBUS is a fieldbus communication protocol known for its real-time capabilities and widespread use in various industrial applications. It adopts a master-slave architecture and is characterized by high reliability.
Modbus Overview: Modbus, on the other hand, is a widely adopted serial communication protocol in industrial automation. It is known for its simplicity and cost-effectiveness, making it a popular choice in a variety of applications.
Communication technology: PROFIBUS uses fieldbus technology, usually using a master-slave architecture, while Modbus is a serial communication protocol that can run in a master-slave or point-to-point architecture.
Data transfer speed: Compared to Modbus, PROFIBUS generally supports higher data transfer speeds and is suitable for applications where real-time communication is critical.
Flexibility and Simplicity: Modbus is generally preferred for its simplicity, ease of implementation, and cost-effectiveness. It’s ideal for applications that don’t require advanced features.
Integration with other systems: PROFIBUS, as a fieldbus protocol, provides better integration with other fieldbus systems and higher-level enterprise networks. Modbus is typically used in stand-alone applications where simplicity and reliability are prioritized.
Application Notes: The choice between PROFIBUS and Modbus depends on specific application requirements, budget constraints, and the level of communication complexity required. PROFIBUS is preferred in complex industrial automation setups, while Modbus is typically used in simpler applications.
Both PROFIBUS and Modbus have their own advantages and applications. PROFIBUS is ideal for high-performance industrial networks, while Modbus offers a simpler solution suitable for a variety of applications, especially in small industrial settings.
Energy meters using Profibus communication protocol, such as MCM2400, APM-96Z Y J Q, and other products, provide many advantages for energy management systems. The following are some of the key points:
MCM2400: MCM2400 realizes real-time data exchange through Profibus, transmits energy consumption and other information to the control center, and realizes real-time monitoring of energy.
APM-96Z Y J Q: The APM series energy meter uses Profibus communication to enable energy data to be transmitted to the monitoring system in a timely manner, ensuring real-time and accuracy.
MCM2400: Utilizing Profibus communication, MCM2400 supports seamless integration with other automation equipment to achieve efficient energy management and optimization.
APM-96Z Y J Q: The APM series realizes collaborative operation between devices through Profibus, providing a high degree of flexibility and intelligence for energy management.
MCM2400: Through Profibus, MCM2400 realizes remote monitoring and control of energy meters, allowing operation and maintenance personnel to remotely adjust equipment parameters and improve operating efficiency.
APM-96Z Y J Q: The APM series can communicate remotely with the monitoring system through Profibus, allowing energy managers to monitor and adjust energy consumption in real time.
MCM2400: Utilizing the powerful performance of Profibus communication, MCM2400 can realize fault diagnosis and prediction of energy meters and improve the reliability of the equipment.
APM-96Z Y J Q: The APM series supports advanced fault diagnosis functions through Profibus, allowing the equipment operating status to be predicted and processed in a timely manner.
MCM2400: MCM2400 provides a flexible communication structure through Profibus, supports plug-and-play of equipment, and facilitates system expansion and upgrade.
APM-96Z Y J Q: The Profibus communication of the APM series supports flexible configuration and scalability of equipment to adapt to changing energy management needs.
MCM2400: Using Profibus communication, MCM2400 can interoperate with other devices that follow the same standards to achieve seamless integration between devices.
APM-96Z Y J Q: The Profibus communication of the APM series ensures the consistency of the energy meter with other Profibus-compatible devices, forming a unified communication standard.
In energy meters such as MCM2400 and APM-96Z Y J Q that comprehensively utilize Profibus communication, these advantages together provide a more intelligent, efficient and reliable solution for industrial energy management systems.
What is Blue Jay Technology Electric meter lifespan? It is between 5 years and 10 years. besides, you can learn the factors that affect the electric meter lifespan.
Abstract: This article will introduce the RS485 communication protocol from its definition, features, application, etc.
How does an electric meter work? You’ve probably stared